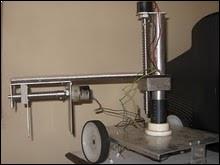
Project Cost: 11,500
Project Code: 1220

Description of the project:
This 3 Axis Pick and Place Robot project is also called a Pick and Drop robot since it has a pick-and-drop robotic arm.
Operating Modes: This project is available in 4 operating modes
- Keypad controlled (wired control)
- Mobile operated using DTMF controlling (wireless control through mobile calling)
- Android mobile controlled using Bluetooth Technology (wireless control)
- PC-operated (wired or wireless, both options are available)
Mechanical Design of the Robot:
This pick-and-place robot has three main mechanical parts/components:
- Robotic arm to hold and release the object
- Lead screw assembly to move the arm up and down
- The chassis of the Robot with wheels to move forward, reverse, left, and right
Dimensions of the Robot:
- Robot chassis base – 25 cm by 25 cm
- Vertical lead screw assembly – 18 cm
- Arm length – 30 cm
- Pick and place gripper length – 15 cm
Please note that these sizes may vary depending upon the modifications done in order to increase performance or reduce the weight of the Robot. If you need any specific dimensions then please email us or call us.
Video – Mobile controlled Pick and place Robot
Block Diagram of the 3 Axis Pick and Place Robot:
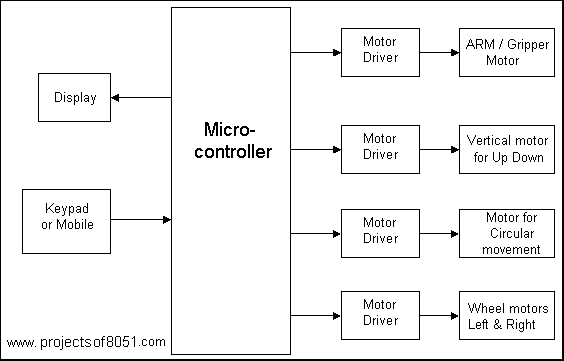
You will the following documents with this project:
- Project Report in pdf format and in word format ( .doc or .docx )
- Circuit diagram
- PCB layout
- Microcontroller Program in assembly language
- Hex file of the microcontroller code
- Datasheets of all the components / ICs used in the project
- Power point presentation / PPT file
Project Photographs:
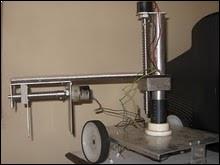
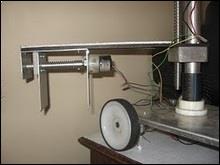
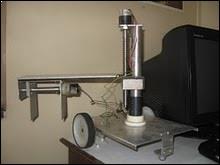
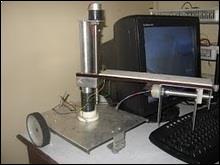
A detailed description of the 3 Axis Pick and Place Robot:
Operation of the Robot:
- Initially, Robot is at a rest position, i.e. state when all motors are stopped and no object is picked or placed.
- Once the power supply is turned on, the microcontroller will wait for a signal from the DTMF decoder which is connected to a mobile phone.
- A User can send various instructions to the robot by dialing a call to the mobile phone which is connected to Robot.
- When the microcontroller gets a signal to pick the object, it moves the gripper motor in say clockwise direction for a fixed time
- When a user gives a command to move the arm in the Up direction then a vertical motor moves in a clockwise direction due to which the whole arm moves towards or away from the picking an object.
- Once user realizes that object is picked then he/she can give command to close the grip. Then gripper motor stops to hold the object by closing jaw
- User can give command to move arm in UP direction and now vertical motor is started in say clockwise direction. This motor also, is on for particular fixed time instant.
- Now user can give command to move the Robot in forward or reverse direction. Depending on command wheel motor is moved in forward or opposite (here anticlockwise) direction till the time it reaches the placing platform.
- As it reaches placing platform, user can give command sequence to release object the motor M1 stops and M2 is switched ON in opposite (here anticlockwise) direction till it releases object properly on desired place.
DC Motors and Motor Driver:
We have used 5 DC motors in this project. Motor driver IC is used because the microcontroller is not able to drive DC motors directly. So output signal of the microcontroller is given to Motor Driver ICs and the output of the driver is given to DC motors.
Applications and Advantages of 3 Axis Pick and Place Robot:
- It can be used in the Production industry.
- In mass production.
- In Automobile Industry.
Future Development:
- Bottle filling Plant.
- Construction works.
Questions and answers about this project:
Question: Can we provide stepper motors instead of DC motors? what is the advantage of using a stepper motor?
Answer: No, we can not provide stepper motor. Reason behind this is, stepper motor has very less torque (and force is proportional to the torque) Since we need high power / force to drive the robot, like gripper, up down motion, we need high torque motors. DC motor provides the necessary torque.
Question: How you are going to send the project through courier in assembled mode or disassembled?
Answer : It is not possible to send in assembled mode. So we will disassemble it and then send by courier.
Question: Can we operate this project using mobile but without calling?
Answer : Yes you can do it by directly pressing the keys which is a wired control or by using a bluetooth device which will be a wireless control.
Can u pease send me ,, “pick and place robot” this robot which things are picked please give me example and how much mass capacity on this robot and how much weight things it’s picked???? Please send me…
Hi Punith, This robot is only for demo purpose. So it has less capacity. Currently it is designed to pick around 200 gram weight.
Hello sir/ma’m,
This robot are movable? And please send me distance between pick flatfish to placed platform…
what is it’s degree of freedom?
what is the diameter of motor ,what is diamter,length of arm,what is the rpm ,torque.
I would like to purchase this project , may i know the procedure for the purchase (how to bank in) due to i am oversea (from Malaysia).
I want to the result analysis in my robot arm to another robot project, in time, distance, torque, current this information is table format please sent this format other robot project
is this project for mechanical students? this project involves most of mechanical parts.. how i can use it for my project? I am a electronics student.. do we can add abyte of electronics part to it?
Do you provide that cable ?
Do you mention all possible procedures to give command in cd?
Hello sir…
in this project, DC motor is used. Is this a toy DC motor or a different one??.If it is a toy 12 volt DC motor, can toy DC motor able to drive robotic arm???
I am making same project with 3 DC motors
hi there,
I am studying in canada and I want to make this project using Audrino Controller instead of 8051. Is it possible?
Can you parcel it to us in canada?
Thank You,
Jay Prajapati
can you send me servo motors details which are used there means cost,specification’s etc
Can we use other techniques instead of DTMF?
And servo motors instead of DC motor?